July 19, 2021
The COVID-19 pandemic introduced several challenges for the automotive industry – from fluctuating demand, to parts shortages, to labor shortages. Case in point: In the beginning of the pandemic, when demand for automobiles dropped, manufacturers reduced shifts and implemented temporary plant closures, furloughs, and layoffs. But now that demand is returning, those same manufacturers are having difficulty filling job openings. And although parts shortages – especially those involving semiconductor chips and other components – are predicted to ease in the latter half of 2021 and through 2022, labor shortages could remain for longer.
The combination of an uptick in demand and difficulty filling open labor positions has led many automotive manufacturers and industry suppliers to investigate new ways to automate their manufacturing processes, including the application of fluid on glass and plastic components during assembly. In addition, the pandemic has highlighted the importance of delivering value to the customer – which, in the automotive industry often comes in the form of improved quality, better safety features, and a wider range of options. The way to do this while maintaining productive and profitable operations, is through automation.
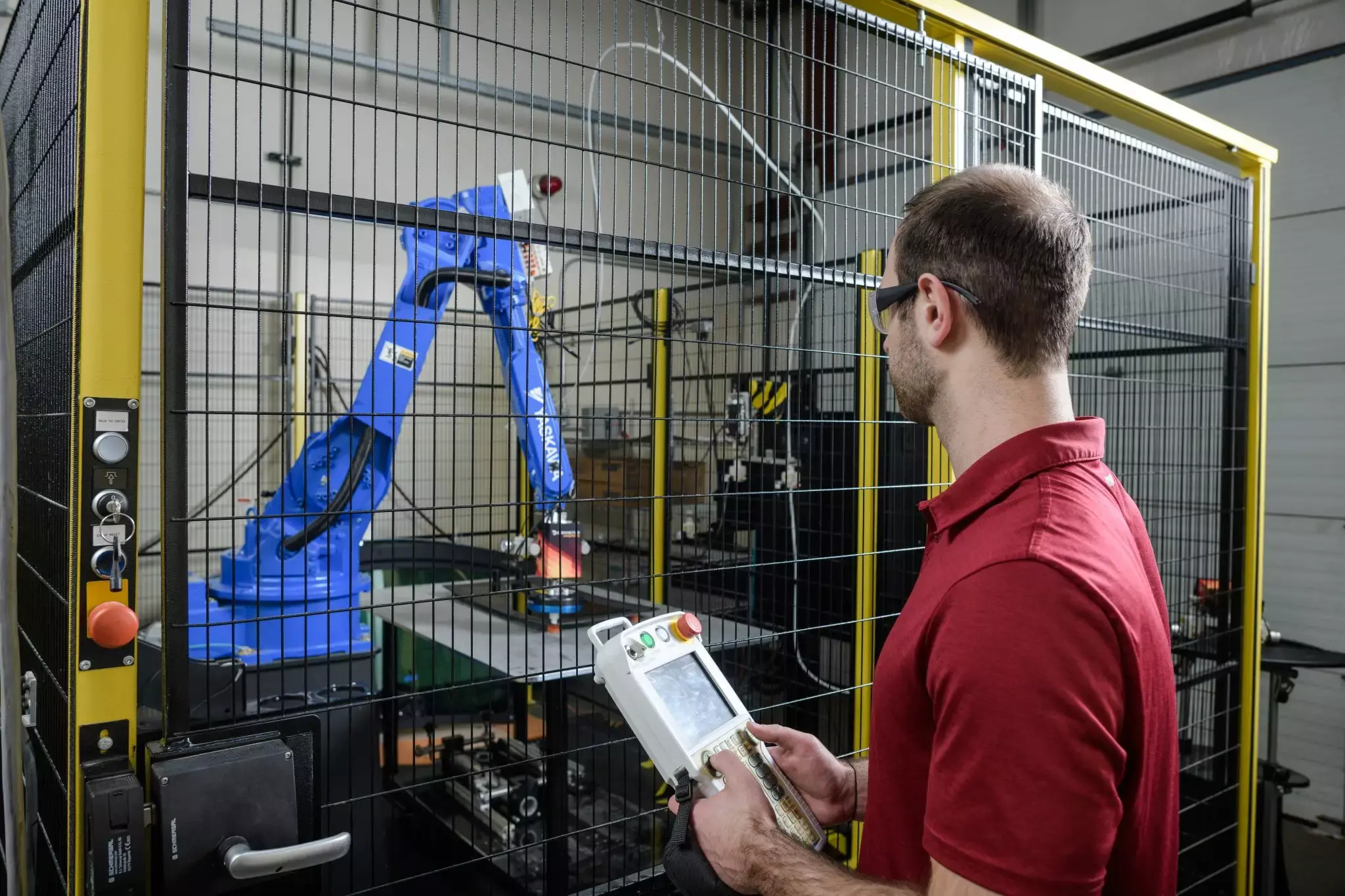
Automation can support lean initiatives by promoting standardization and reducing opportunities for errors.
Congratulations are in order: our very own Sydney Spraw, Ph.D., president of Designetics, has been named a finalist for the Entrepreneur of the Year® 2021 Michigan and Northwest Ohio Award. This prestigious award recognizes business leaders whose drive, acumen and ingenuity position their business for success and growth now and into the future.
According to Ernst & Young, the creators of the award competition that is now in its 35th year, the Entrepreneur Of The Year is one of the preeminent competitive award programs for entrepreneurs and leaders of high-growth companies. The nominees are evaluated by an independent panel of judges on six criteria: entrepreneurial leadership; talent management; degree of difficulty; financial performance; societal impact and building a values-based company; and originality, innovation and future plans. Since its inception, the program has expanded to recognize business leaders in more than 145 cities in 60 countries around the world.
The award winners will be announced during a special virtual celebration on Thursday, August 5 at 6:00 p.m. ET and will become lifetime members of a community of Entrepreneur Of The Year alumni from around the world.
“I’m deeply honored and humbled to be nominated for such a prestigious award,” Spraw says. “As an entrepreneur, I’m keenly aware of the challenges and struggles facing businesses today, and I’m heartened by the dedication and commitment to excellence Designetics’ employees have exhibited during these unprecedented times. That makes this nomination all the more special.”
Regional award winners are eligible for consideration for the Entrepreneur Of The Year National Awards, which will be announced in November of 2021. The Entrepreneur Of The Year National Overall Award winner will move on to compete for the EY World Entrepreneur Of The Year™ Award in June, 2022.
In industries as diverse as automotive, aerospace, and consumer goods, the proper application of fluid to a substrate can be an important factor in product quality, performance, and even safety. This is why at Designetics, we focus on manufacturing applicators and automated systems that provide the highest accuracy and consistency in fluid application. And now, to help our customers monitor, inspect, and record their critical fluid application processes, we’ve partnered with Coherix – the leader in machine vision 3D process control solutions for fluid dispensing – to develop the Ce360 path scanner for quality inspection.
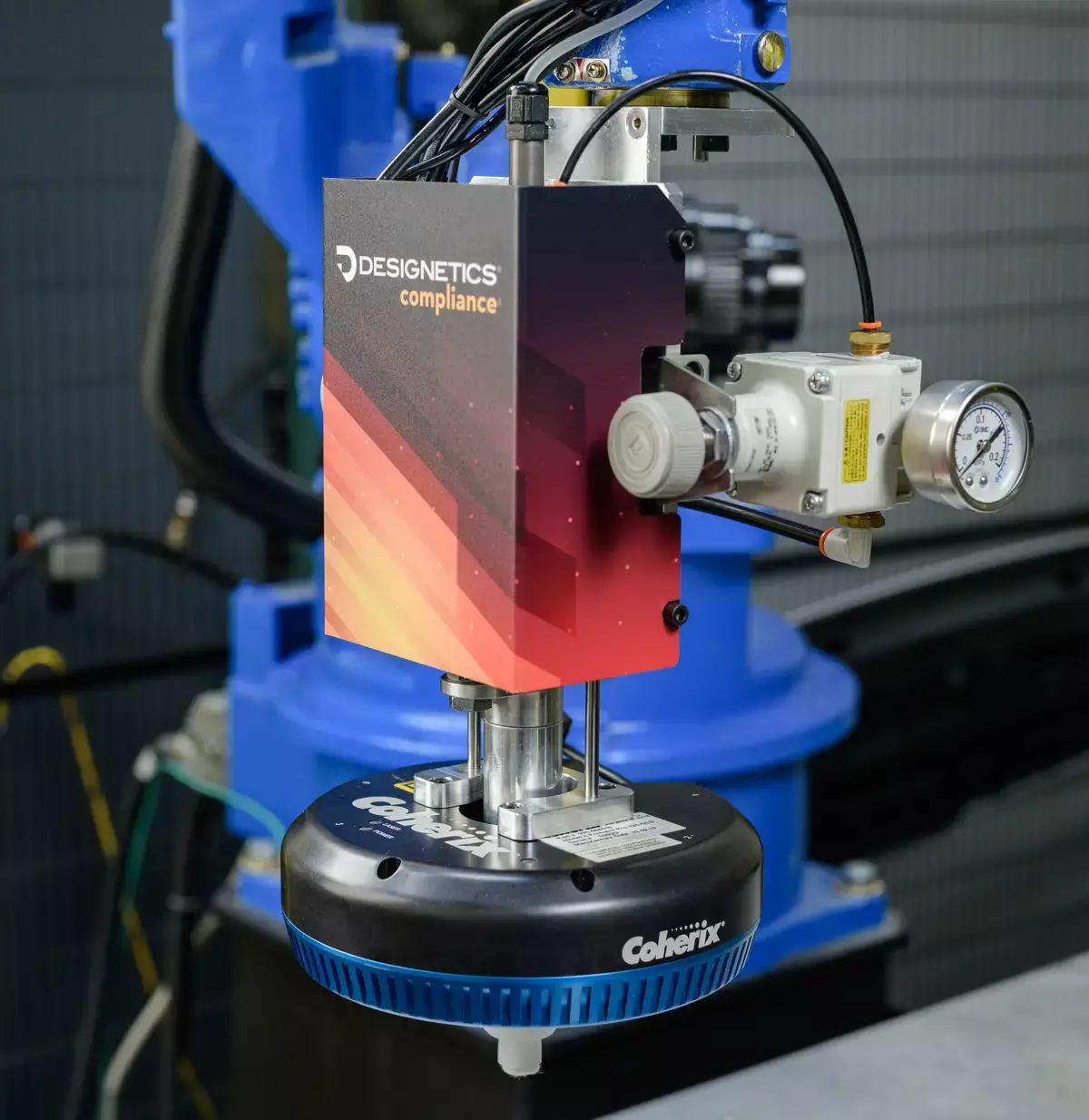
The Ce360 provides reliable, consistent, 3D quality inspection and recording of the fluid dispense path.
May 24, 2021
Designetics Honored as Industry Leader
Further cementing its reputation as the preeminent provider of fluid applications and systems, Designetics was recently honored as a top Industrial Adhesives Solution Provider for 2021 by Manufacturing Outlook magazine. Annually, the magazine selects ten companies that are “at the forefront of providing industrial adhesives solutions and transforming businesses.”
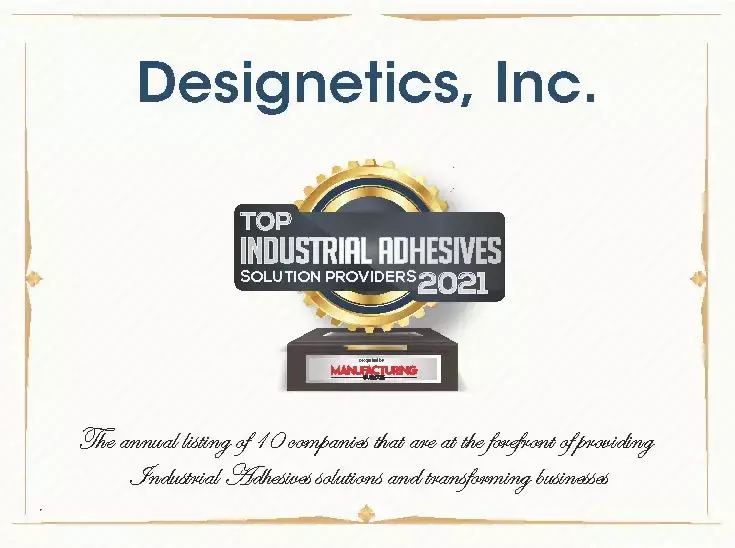
Designetics has long been acknowledged as creating the fluid applications industry, as, in the 1980s, it worked with automotive manufacturers to create a more efficient way of applying adhesives to assembly line automotive windshields. In creating applicators that performed to exacting measures on a repeatable basis, Designetics spawned a new way of helping a wide variety of manufacturers advance their business interests while allowing for more technical assembly.
When the worldwide pandemic truncated the 2020 Major League Baseball season and eliminated the entirety of the Minor League Baseball season, many fans, players and pundits were left to wonder if there would be a viable 2021 season. But careful measures and a focus on safety have given new life to baseball in 2021. And the Toledo Mud Hens are no exception.