Automation Your Process
In fact, automation and lean initiatives often go hand-in-hand. Automating a process supports the lean principle of standardization and reduces the opportunities for errors or quality defects, while freeing up humans to do more value-added work. Take an example from one of Designetics product offerings. Our semi- and fully automated fluid application systems typically use an applicator track for delivering new applicators to the robot’s end of arm tool, or to a semi-automated handheld remote. The applicator track was designed with several poka-yoke – or mistake-proofing – design features that support lean manufacturing.
First, the applicator track includes two sensors – one that monitors if the applicator track is low on applicators, which could cause a situation where the next applicator to be picked by the robot isn’t in the correct location, and a second sensor that ensures the next applicator is in the correct position. If either condition is present – if the track is low on applicators, or if the next applicator isn’t in the correct position – a signal is sent to the robot controller, so the robot can halt movement or take other corrective action to avoid a collision.
The other poka-yoke design feature of the applicator track ensures that applicators can only be loaded into the track in a specific orientation. This ensures the robot doesn’t acquire an applicator that’s skewed or misplaced, which would result in the width or path of fluid application being incorrect.
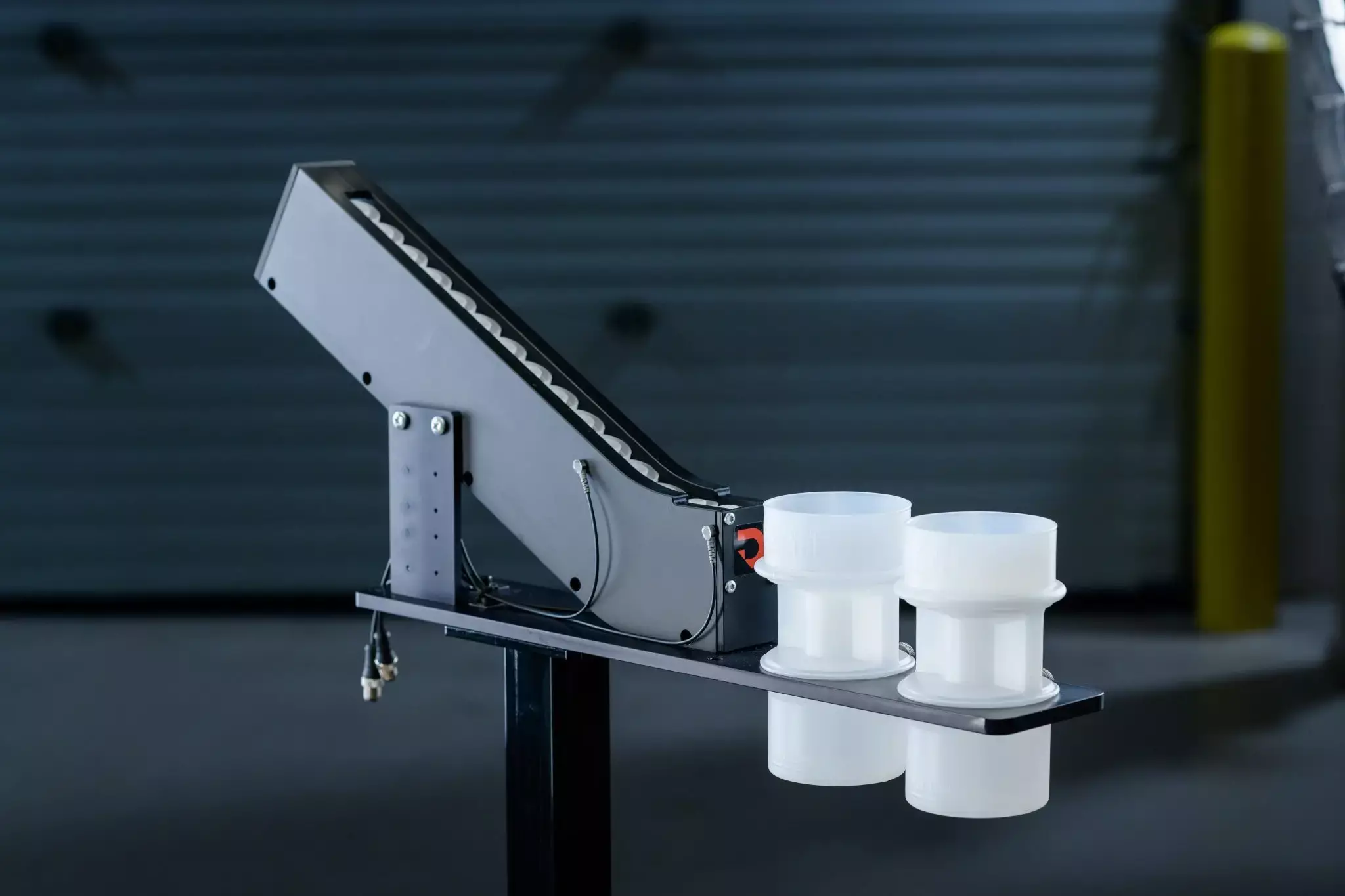
Designetics applicator track was designed with lean manufacturing principles in mind.
The COVID-19 pandemic has forced many industries – including automotive manufacturing – to adapt to doing more with less, especially when it comes to labor. In many cases, the solution has been to place a stronger focus on lean manufacturing principles and automation – both of which can help increase value to the customer by improving productivity and quality.
Helping Companies Create Automated Fluid Application Systems
Designetics has helped numerous companies in the automotive industry navigate the move from manual or semi-automated fluid application to fully automated application systems – before and during the COVID-19 pandemic. We know what it takes, from implementing the automated system and customizing it to your process, to training workers, to defining the return on investment. If you’d like to learn how Designetics automated fluid application systems can help improve productivity and quality, give us a call.