Working with an Adhesion Promoter: Application is Key to Effectiveness
Like the adhesive, the adhesion promoter must be applied to the customer’s exact specifications – too little means the adhesive may not form a proper bond between the surfaces, leading to shorter life of the product or even structural failure. On the other hand, over-application of the adhesion promoter can not only be detrimental to the adhesive’s ability to bond the materials, it also increases application cycle time and reduces productivity.
This is why the ability to apply films in a very thin layer – and to do so with high accuracy and repeatability – is critical in adhesive applications. At Designetics, we have expertise in all types of fluid applicators and dispensing equipment to efficiently and repeatedly apply fluids to substrates – with the right thickness and accuracy for the application. Whether the parts being joined are glass, metal, or – in the case of most tape adhesives – plastic, we have experience with virtually every combination of materials and adhesion promoters imaginable.
Imagine if you were admiring your new vehicle, just a few days old, and noticed that a piece of exterior molding was already coming loose… Or if you were out on your morning run, several miles from home, and the sole of your sneaker came apart…
These are real-world scenarios that can happen when an adhesion promoter isn’t properly applied – in the right amount and with the right accuracy. Designetics’ manual, semi-automated, and fully automated fluid applicators help manufacturers of everything from automobiles to appliances improve accuracy in their manufacturing process and avoid these costly quality issues.
Ready for Semi-Automated or Fully Automated Production?
If you’re ready to take the next step, into semi-automated or fully automated production, Designetics can help. Our automated and semi-automated fluid application systems provide superior coverage and optimal application of wide range of fluids in a completely closed system. This means the system is air-tight throughout – from the bottle to the , to the end-of-arm-tooling, right to the applicator – at every junction. And a single piece of tubing serves the entire fluid flow, eliminating connections that could allow air to enter the system. What does this mean for you? It means your fluids – especially adhesion promoters – last longer without the drying effects of air. Quality problems due to drips or leaks are eliminated, and with no contact between the chemicals and mechanical equipment, maintenance is significantly reduced. It also means that detrimental effects to employees or the environment are virtually eliminated, since exposure to harmful solvent-based fluids is minimized.
A Step-By-Step Approach
If you’re applying an adhesion promoter in your manufacturing process, contact us to see how we can help you improve quality and reduce production time. With over 5000 applicators and systems, we have a solution for virtually every combination of materials and adhesion promoters imaginable. But we don’t profess to know it all – we’re learning about new fluids and requirements with every application we tackle. We love new product innovation and welcome the idea of new markets and practices based on your process.
Case in point: For each application, we consult with you to choose the best fluid applicator for your specific fluid viscosity, surface roughness, and accuracy requirements. And if one of our existing applicators isn’t the perfect solution, our in-house rapid prototyping capabilities allow us to quickly provide you with a custom applicator. Our aim is to develop the best solution the first time, so we work closely with our internal R&D team to supply an applicator solution that exceeds your expectations for accuracy, ease-of-use, and quality. And once we’ve dialed-in the perfect solution, we make the production parts in-house, for full control over quality and lead time. This means you get the fluid applicator that exactly fits your needs, directly from the designers and manufacturer who understand your goals and challenges.
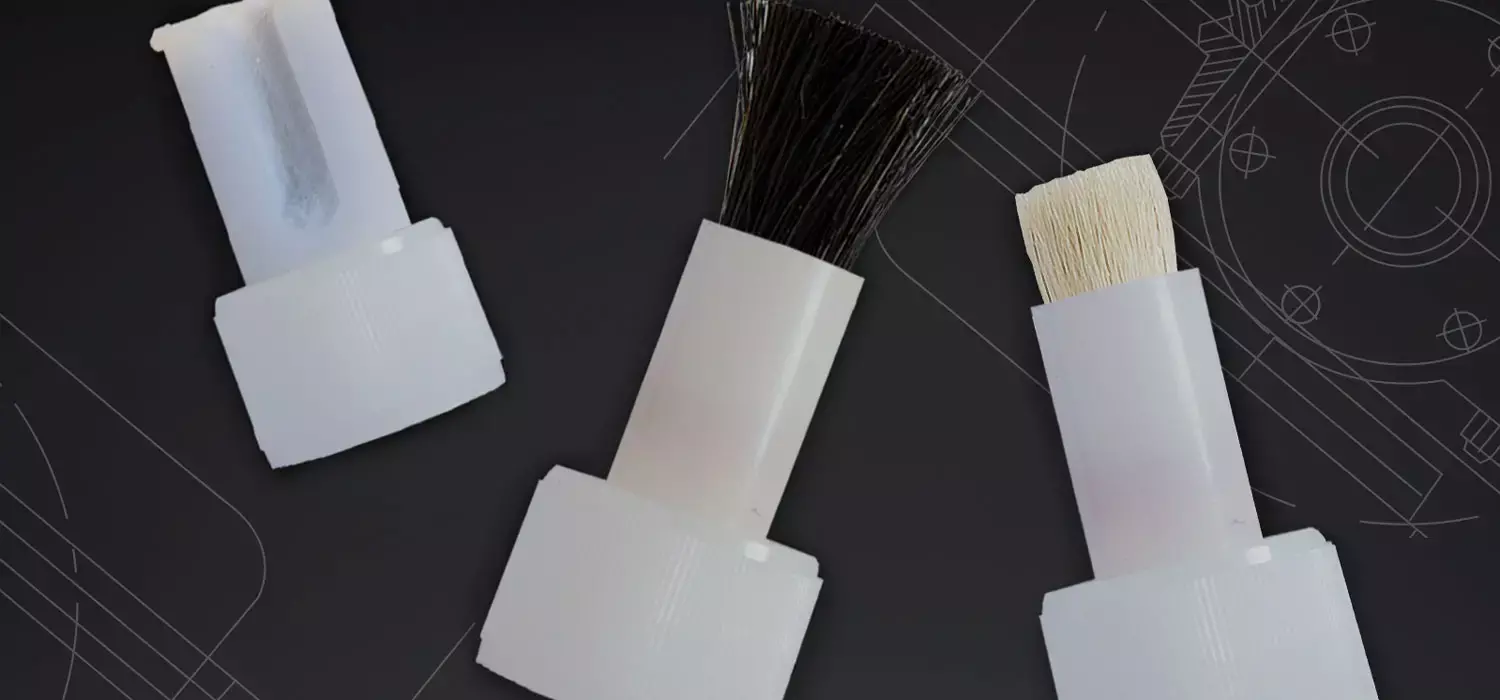
For more information on our hand-held fluid applicators and automated applicator systems, check out this video. If you want to learn how to improve the application and effectiveness of adhesion promoters, please contact us. We would love to learn about your process and find a way to help you get perfect, repeatable fluid application results every time.