We Customize Solutions For Your Challenge
We offer applicators made from a wide range of materials – including felt, synthetic and natural hair, sponge, foam and rubber – and in a range of shapes. But our engineers and designers understand that just choosing an applicator or system that will work for your fluid and substrate doesn’t mean it will be the most effective or efficient solution. For example, two substrates made from the same material but with different surface roughness might require different applicator materials. Our exploratory process also helps us determine what applicator shape is best for your substrate and process. Whether it’s a traditional brush applicator, a channel-type applicator for coating the inside of a part, or a wrap-around applicator to coat multiple surfaces at once, we’re experts at tackling difficult or unusual substrate geometries.
Asking the right questions – about your application, process, and challenges – ensures that our solution meets or exceeds your expectations. These questions also help us identify opportunities for improvement – better accuracy or increased throughput, for example – that might have otherwise been overlooked.
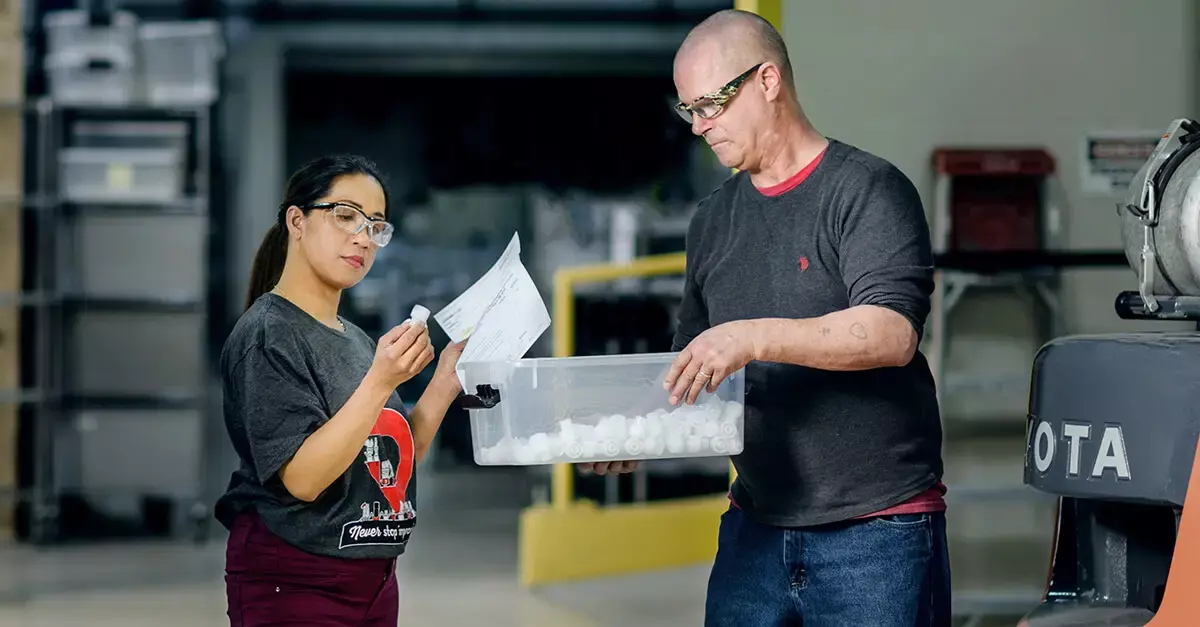
Asking the right questions – about your application, process, and challenges – ensures that our solution meets or exceeds your expectations.
Standard or Custom, Manual or Automated?
If we determine that a custom applicator is the best solution for your specific fluid, substrate, or accuracy requirements, our in-house, rapid prototyping process ensures that we can get parts in your hands within days, so you can begin testing. We also replicate your process and conduct our own in-house testing to iterate and improve our designs, ensuring that the final product will perform exactly as expected, and consistently, in your real-world conditions.
When a semi-automated or fully automated process is the best solution, we have a wide range of fluid application systems and accessories, so we can recommend a solution that will meet your needs not only for the fluid application, but also for ease of use, flexibility, and safety. And just like we do with manual applicators, we test each semi-automated or automated system with your specific fluid and substrate to ensure it meets your requirements for fluid flow and application precision.
Our exploratory process involves asking questions and listening to your needs, and although it’s comprehensive, our expertise means that it isn’t time-consuming. If you’re ready to get started on your next fluid application project – whether manual or automated – schedule a consultation or fill out our prototype request form, and we’ll reach out quickly to get you on the path to accurate, repeatable fluid application.