What is a Peristaltic Pump?
A peristaltic pump is a type of positive displacement pump that uses rotating rollers, or shoes, to compress and move a flexible tube or hose, creating a flow of fluid. The rollers compress the tube in a wave-like motion, similar to the way food is moved through the digestive system, hence the name “peristaltic.”
This type of pump is typically used for low-flow, high-pressure applications, such as in laboratory settings or for dispensing small volumes of liquid. One of the key advantages of a peristaltic pump is that it doesn’t come into contact with the fluid being pumped, making it ideal for handling delicate or sensitive materials. Peristaltic pumps are easy to clean and maintain, making them a popular choice in food and beverage, medical and chemical industries.
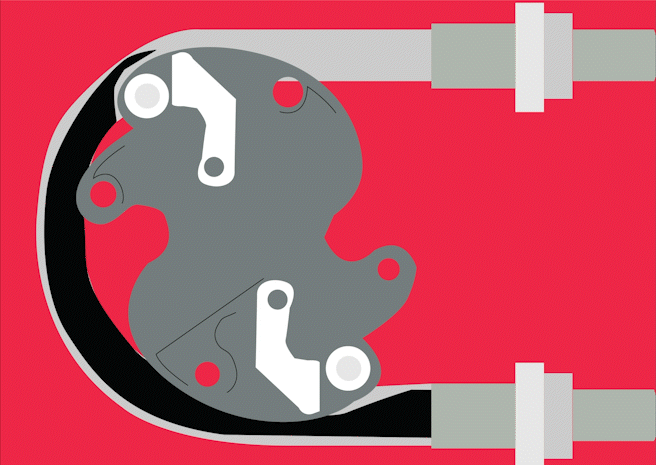
How does a Peristaltic Pump Work?
The flow of fluid through a peristaltic pump is driven by a series of rollers mounted on a rotor that rotates inside a pump housing. The flexible tube or hose is positioned between the rollers and the housing, with one end of the tube connected to the inlet of the pump and the other end connected to the outlet.
As the rotor rotates, the rollers compress the tube. This compression creates a pressure difference between the inlet and outlet of the pump, which causes the fluid to flow through. The fluid is pushed out of the inlet and into the outlet by the action of the rollers.
The rate of flow can be adjusted by varying the speed of the rotor, the size of the rollers or the size of the tube or hose. Peristaltic pumps can be designed to handle different types of fluids and can be constructed with various materials to meet specific requirements. Some peristaltic pumps are self-priming, which means they can pump fluid from a container without having to first fill the tube with liquid.
Peristaltic Pump Advantages
Flow Regulation
Their ability to produce a constant flow at differing speed and pressure is a key feature of positive displacement pumps. These pumps regulate flow by adjusting the speed of the rotor, the size of the rollers or the size of the tube or hose.
Peristaltic pumps like the Designetics e3 series fluid dispense systems are equipped with a control system that can monitor and adjust the flow-rate in real time. “This balance of ‘feed and speed’ is especially important in fluid application,” said Mark Moll, Designetics senior project manager. “Our pumping technology allows you to dial in the exact speed controls necessary—right down to the RPM.”
Speed Control
The flow rate in a peristaltic pump is determined by the speed and quantity of the rollers, which can vary for a given pump size and tube diameter. The speed of the rollers, also known as the rotor, determines how often the tube is compressed and the quantity of rollers determines how much of the tube is compressed at once. Together, these two factors indicate how much fluid is moved through the tube per unit of time—a.k.a. the flow rate.
Designetics offers a range of automated fluid applicator systems, such as the e3mini and e3multi, that provide different options for controlling the flow rate. These systems offer three different motor options that can accommodate a range of speeds. The first option is 3 to 60 rpm, which is suitable for low-flow applications that require precision and accuracy. The second option is 5 to 115 rpm, which is suitable for medium-flow applications that require a balance of precision and speed. The third option is 15 to 250 rpm, which is suitable for high-flow applications that require speed and efficiency.
“Our newest automated dispensing system—the e3 minimax—is powered by a servo motor that runs from 0 to 250 rpm. It uses the same type of pump and motor for both high-speed and low-speed applications involving low-viscosity fluids,” says Moll.
Low Shear
The relative motion between layers of fluid is known as shear. When dispensing fluids of varying viscosity, it’s important to consider how shear can impact the quality of the application. Viscous fluids such as pastes, gels and heavy oils tend to be more sensitive to shear than less viscous fluids, such as water or light oils. High shear rates can cause viscous fluids to break down, resulting in poor quality, uneven applications.
Peristaltic pumps are well-suited for dispensing fluids of varying viscosity because they move fluids gently to reduce any breakage between layers. This results in a smooth, consistent flow of fluid with minimal shear.
Contamination Free
The design of the peristaltic pump is ideal for corrosive fluids because it puts only the pumping tube in contact with the material. The fluid travels directly through an air-tight system from the storage container or bottle to the pump to the applicator, with no connections that allow for drips or leaks. This eliminates the need for any additional seals or gaskets that could wear out over time or become damaged by the corrosive nature of the fluid.
Designetics pumping systems, like the e3mini and e3multi, are designed to protect the fluid and the operator. The fluid is protected from air exposure and the operator is protected from chemical exposure. The pump and control unit are engineered to be user-friendly, with easy-to-use interfaces and safety features such as over-temperature protection and emergency stop buttons.
Low Maintenance
The lack of valves, seals, propellers or tanks in a peristaltic pump makes it very low maintenance compared to other types of pumps. Since the flexible tubing is the only part of the pump that comes into contact with the fluid, maintenance is as simple as replacing the tubing when it becomes worn or damaged. There’s also no need to clean or disinfect internal parts, which can be time consuming and costly.
The standard tubing used by Designetics is compatible with most low-viscosity fluids and chemicals. If your unique application requires additional testing, we’ll examine the compatibility and performance in-house until we find an option that meets your needs.
Our System Compatibility
Our fluid dispensing systems are designed with precision and reliability in mind, catering to a wide range of fluids and substrates. When paired with our specialized applicators, these automated and semi-automated systems can enhance productivity and protect workers, all while satisfying your unique fluid dispensing needs.
“Depending on your needs, you’ll have the option of upgrading a semi-automated system to a fully automated system with the exact same unit,” said Moll. “It’s as easy as adjusting a couple of settings and adding an air compliance and applicator track.”
Wrap Up
Designetics creates fluid application systems and solutions using advanced technology for the most accurate, precise and dependable dispensing of virtually any fluid on any substrate.
For more information, please reach out to us today. We’re ready to discuss your challenges and help you find the best solution.