Consistent, Safe, and Maintenance-Free
An anti-rotate, non-slip applicator adapter on the Precision Air Compliance ensures that the applicator will maintain its mounted orientation, so there’s no need for periodic checks to ensure the applicator is in the proper orientation. For example, if the applicator design includes a flat that is mounted perpendicular to the air compliance unit, it will remain in that orientation throughout the process, with no slipping or rotating.
We’ve also developed the Precision Air Compliance with safety and ease-of-use in mind. First, the tubing from the pumping system – which can be any of our e3 fluid application systems – is simply routed through the air compliance unit, so no additional connections are needed. This eliminates the possibility of leaks or drips that could cause quality issues or safety hazards. And because the fluid only comes into contact with the tubing, the Precision Air Compliance requires no maintenance for cleaning or replacement of parts due to fluid exposure.
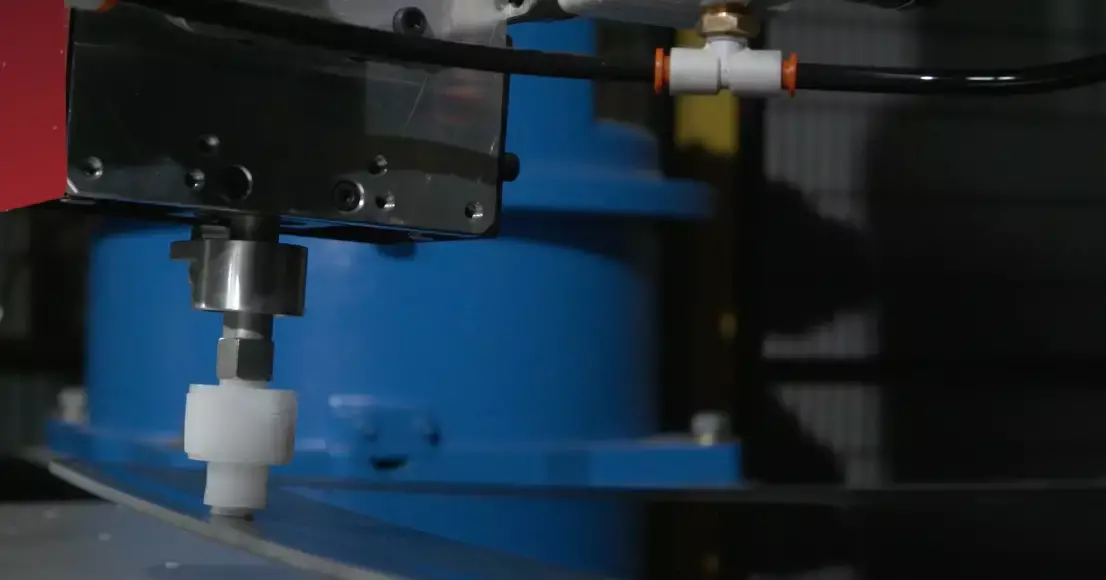
The adaptor for the Precision Air Compliance has been designed to fit all Designetics applicators.
Promoting Automation by Eliminating Unnecessary Production Steps
In any fluid application system, the applicator will eventually need to be replaced – due to a change in the pumped fluid or simply because the current applicator has reached its end of useful life. The typical methods to change out an applicator are either manually – an operator removes the applicator by hand and installs a new one – or, in an automated system, a “fork” type device is used to remove the applicator. But the Precision Air Compliance includes an “applicator strip” function that eliminates the need for manual intervention or unnecessary production steps.
The applicator strip function uses an air cylinder to simply eject the applicator from the adaptor. The robot or automated system can then pick a new applicator from an Applicator Track. The cylinder also includes sensors that indicate whether it is extended or retracted. These sensors are wired to the main control panel so the robot or automated system can be programmed to remain stationary when the cylinder is extended, preventing the possibility of a “crash” due to robot movement before the cylinder is retracted. This allows a production to run continuously without intervention, for higher throughput and better safety for operators.
Consistent, Repeatable Fluid Application with the Precision Air Compliance
Whether your fluid application process is manual, semi-automated, or fully automated, Designetics has a fluid applicator or system that can meet and exceed your expectations for productivity, accuracy, and quality. And for a truly automated solution, with no operator intervention required, our e3 series of fluid application systems paired with our Precision Air Compliance provides unmatched consistency and repeatability in fluid delivery, even in the most challenging applications. To learn how to get flawless results from your fluid application system every time, give us a call.