Reduces Manual Handling Risks & Human Error
Automation significantly minimizes the need for manual handling in manufacturing processes, thereby reducing the risk of injuries related to lifting and moving heavy materials. Automated systems are designed to handle cumbersome tasks that would otherwise pose physical strain to workers. This transition from manual labor to mechanized processes not only enhances efficiency but also significantly lowers the incidence of musculoskeletal disorders, common in tasks involving repetitive motion or heavy lifting.
Furthermore, automation plays a crucial role in reducing human error. By delegating precision-based tasks to machines, the likelihood of mistakes caused by fatigue or inattention is significantly diminished. This ensures consistent quality in manufacturing and drastically reduces the risks associated with errors, contributing to a safer work environment.
Eliminates or Minimizes Accidents & Waste
Automation in manufacturing serves as a key player in accident prevention. Systems like the Bottle Holder with Level Detection exemplify how automation can prevent spills and exposure to harmful substances, safeguarding workers from potential accidents. These systems ensure controlled, safe handling of materials, minimizing the risk of spills or mishandling that could lead to workplace accidents.
Additionally, by automating tasks like fluid level monitoring, workers are freed to engage in more skilled, value-added activities. This not only improves efficiency but also reduces the likelihood of accidents associated with non-specialized tasks. Automation's role in reducing waste is equally significant. By optimizing processes and minimizing errors, automated systems contribute to a more sustainable and environmentally friendly manufacturing approach, further enhancing workplace safety.
Precise and Accurate Manufacturing Processes
Automation ensures precise and accurate manufacturing processes, essential for maintaining high safety standards. Automated systems are programmed for precision, eliminating the variances and inconsistencies common in manual operations. This precision is crucial in manufacturing components that must adhere to strict safety standards, as even minor deviations can compromise the integrity of the final product.
Moreover, accuracy in manufacturing processes reduces the likelihood of errors that could lead to safety hazards. Consistent and accurate production means fewer defective or unsafe products, ensuring that both workers and end-users are protected from potential risks.
Mitigates Hazardous Tasks
Automation in manufacturing plays a crucial role in mitigating hazardous tasks. Here are specific examples of how automation can reduce or eliminate risks:
- Automated fluid dispensing systems reduce exposure to harmful chemicals.
- Robotic arms can handle high-temperature materials, preventing burns.
- Automated quality control minimizes the need for workers to be near fast-moving machinery.
- Enclosed automated systems contain hazardous dust or particles.
- Automated monitoring systems detect unsafe conditions, triggering shutdowns if necessary.
- Programmable machines operate in environments dangerous to humans, such as areas with toxic gases.
- Automated logistics systems reduce the need for manual transportation of heavy goods, lowering the risk of physical injury.
Real-Time Monitoring & Safety Alerts
Automation enables real-time monitoring of manufacturing processes, critical for swiftly identifying and addressing potential safety issues. With sensors and monitoring systems integrated into automated equipment, anomalies or malfunctions can be detected instantly, allowing for quick intervention. This immediate response capability is crucial in preventing accidents and ensuring the safety of workers.
In addition to monitoring, automated systems can be programmed to provide safety alerts. These alerts notify operators of potential hazards, ensuring that preemptive measures are taken to avoid accidents. The combination of real-time monitoring and safety alerts forms a robust safety net, significantly enhancing worker safety in manufacturing environments.
Improve Worker Safety with Automated Fluid Dispensing Systems
The integration of automated fluid dispensing systems stands as a testament to the advancements in manufacturing safety. These systems exemplify how automation can reduce human exposure to hazardous substances and minimize the physical strain associated with manual fluid handling. Implementing such systems ensures a safer and more efficient environment for workers.
Innovative Technologies Designed for Your Process
The interplay between automation and safety is a critical aspect of modern manufacturing. Recognizing that even the most skilled teams are susceptible to human error, our approach focuses on simplifying processes through automation. A prime example of this philosophy in action is our solution for coating or priming cylindrical parts, a task that is both common and challenging in manufacturing. The unique shape of these parts often requires direct handling by operators, which can be cumbersome and unsafe, particularly when dealing with hazardous chemicals.
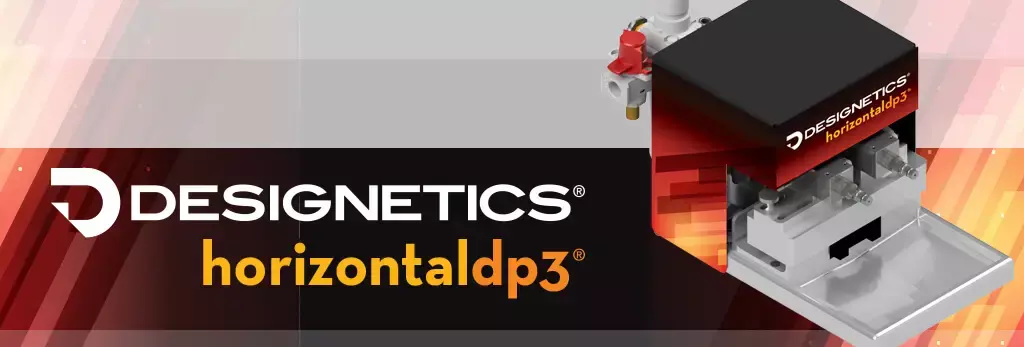
To address this, we developed the Horizontal dp3 automatic flow dispenser. This innovative device revolutionizes the coating process by enabling operators to apply coatings quickly and safely, without direct contact with the parts. These innovations underline our commitment to developing automated solutions that prioritize safety while maintaining simplicity and efficiency. In doing so, we continue to lead in the integration of safety-conscious automation into the manufacturing sector, ensuring that worker protection and productivity go hand in hand. Interested in learning more? Contact us today.