Fluid Monitoring Via Level Sensor
With the level sensor option, the operator inserts the sensor to the desired “low level” depth in the bottle and uses the pump control panel to set the number of run cycles that can be completed after the “low” level has been reached. When the fluid reaches the “low” level, the system sends an alert to the pump control panel or to the customer’s HMI.
This first alert acts as a warning that the bottle is almost empty, so the operator has time to take action when the process allows – without disrupting production – rather than having to immediately stop the process to refill or change the fluid bottle.
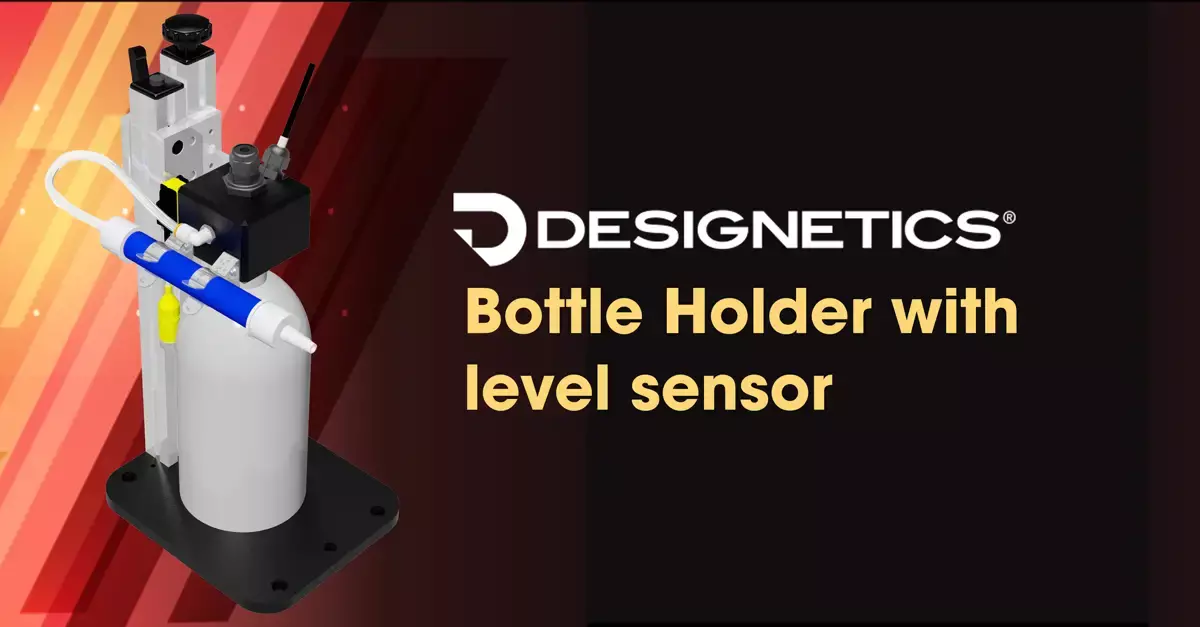
The bottle holder with level sensor is typically used with clear fluids.
If no action is taken and the predetermined number of cycles is completed after the “low” level alert, the system will shut down the pump to ensure that the tubing isn’t damaged and prevent the system from attempting to move fluid from an empty bottle. This eliminates the potential maintenance cost – and time – of replacing tubing or flushing air out of the lines.
Fluid Monitoring Via Load Cell
The load cell monitoring system operates like a scale – it sits under the bottle holder and monitors the weight of the bottle to determine the amount of fluid present. The operator first sets the system to recognize both an empty and a full bottle so that it can determine when the fluid level is at 100 percent (full). Then the operator sets both the percentage at which the system should send a “low level” alarm and the number of run cycles that can be completed after the “low” level has been reached.
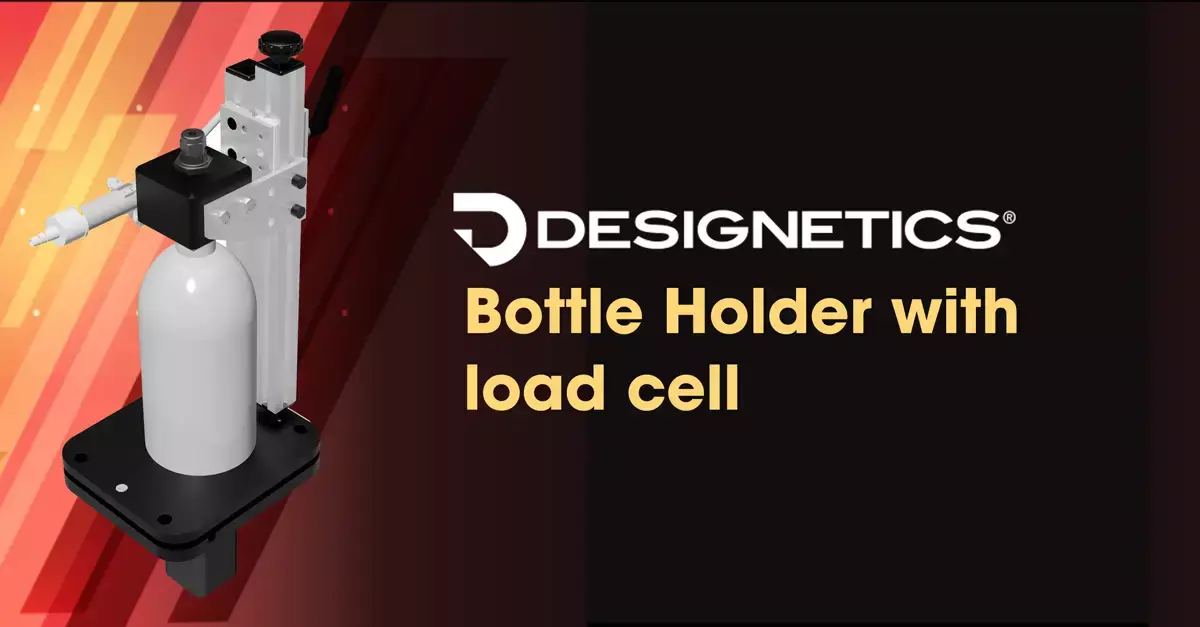
The bottle holder with load cell is used to monitor fluids that aren’t clear and transparent.
Like the level sensor, if the predetermined number of cycles is completed after the “low” level is reached, the load cell system will shut down the pump to prevent unnecessary maintenance or potential damage to the fluid line.
Focus on Value-Add
Monitoring the level of fluid in a bottle is a simple task, but one that your operators shouldn’t have to do. The Bottle Holder with Level Detection frees your operators to focus on value-added work and avoid disrupting production to fill or replace fluid bottles. To learn more about how Designetics fluid application systems can help you eliminate non-value-added work and avoid unnecessary downtime, give us a call or send us a message.