The Importance of Poka Yoke
The importance of poka-yoke lies in its ability to significantly reduce costs associated with quality issues such as scrap, rework, and customer returns. It also improves overall process efficiency by minimizing downtime, increasing throughput, and enhancing employee morale.
Poka-yoke is particularly valuable in complex manufacturing processes where a single error can have far-reaching consequences. For example, in the automotive industry, a mistake during assembly could result in a safety issue that puts lives at risk. Poka-yoke helps prevent such errors by using simple and intuitive design features to guide workers and machines, eliminate sources of variability, and catch mistakes before they result in defects.
Another benefit of poka-yoke is that it empowers workers to focus on higher-value tasks instead of wasting time on error correction or quality inspections. This can lead to increased job satisfaction and engagement, which in turn can improve overall performance and reduce turnover.
Ultimately, the importance of poka-yoke lies in its ability to deliver high-quality products to customers while minimizing costs and maximizing efficiency. By reducing the risk of human error and improving overall process control, manufacturers can stay competitive in a rapidly changing marketplace and meet the demands of increasingly discerning customers.
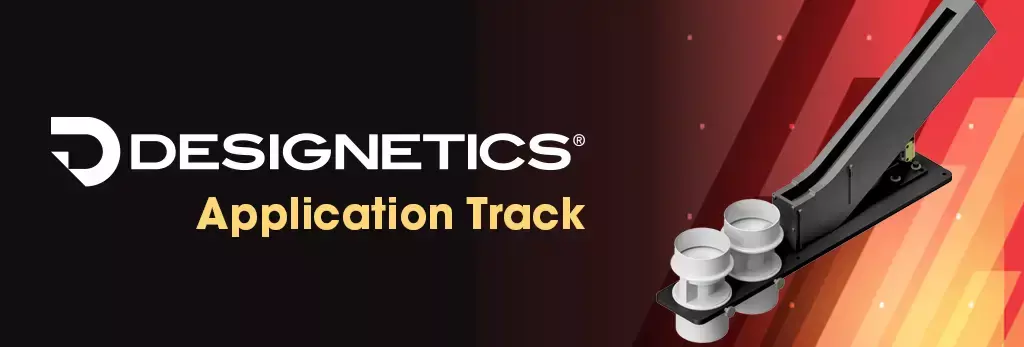
Benefits of This Lean Error-Proofing Process
Reduced Defects: The primary goal of poka-yoke is to prevent errors and defects from occurring in the manufacturing process. This can save time, reduce waste and improve overall product quality. When errors and defects are caught early, they can be corrected before they become major problems that require costly rework or even scrapping of the product.
Increased Efficiency: Poka-yoke can help to improve the efficiency of the manufacturing process by reducing the amount of time and resources that are wasted on correcting mistakes. By minimizing the need for rework and other corrective actions, poka-yoke can help to streamline the manufacturing process and make it more efficient overall.
Improved Safety: Poka-yoke can also help to enhance safety in the manufacturing environment by reducing the risk of accidents and injuries caused by human error. By designing processes and equipment that are inherently safe, poka-yoke can help to prevent accidents and improve worker safety.
Enhanced Customer Satisfaction: By reducing errors and defects, poka-yoke can help to improve customer satisfaction by ensuring that products meet or exceed customer expectations. This can lead to increased customer loyalty and repeat business.
When Should I Use Poka Yoke Manufacturing?
Poka-yoke can be applied to a wide range of manufacturing processes, and can be particularly useful in situations where errors or defects can have serious consequences, such as in the production of medical devices or aerospace components. However, poka-yoke can be applied anywhere errors are a concern. Here are some situations where poka-yoke may be especially useful:
Measurement Errors: Can be prevented with poka-yoke by designing measurement tools that prevent incorrect readings, such as using sensors that only detect specific measurements.
Setup Errors: Can be prevented with poka-yoke by creating systems that automatically detect and correct any setup errors that may occur during the manufacturing process. For example, designing machines that only fit together in one way can help prevent incorrect setups.
Process Errors: Can be prevented with poka-yoke by designing processes that are simple and easy to follow. This can include using visual cues to indicate the correct order of steps or using automated systems that detect errors and correct them in real time.
Operation Errors: Can be prevented with poka-yoke by designing equipment that is difficult to misuse. For example, creating machines with clear and simple controls can help avoid errors caused by operator confusion.
In general, poka-yoke is most effective when it’s applied early in the manufacturing process, as this allows for errors and defects to be caught and corrected before they have a chance to cause serious damage. By implementing poka-yoke, manufacturers can improve efficiency, reduce waste and enhance product quality.
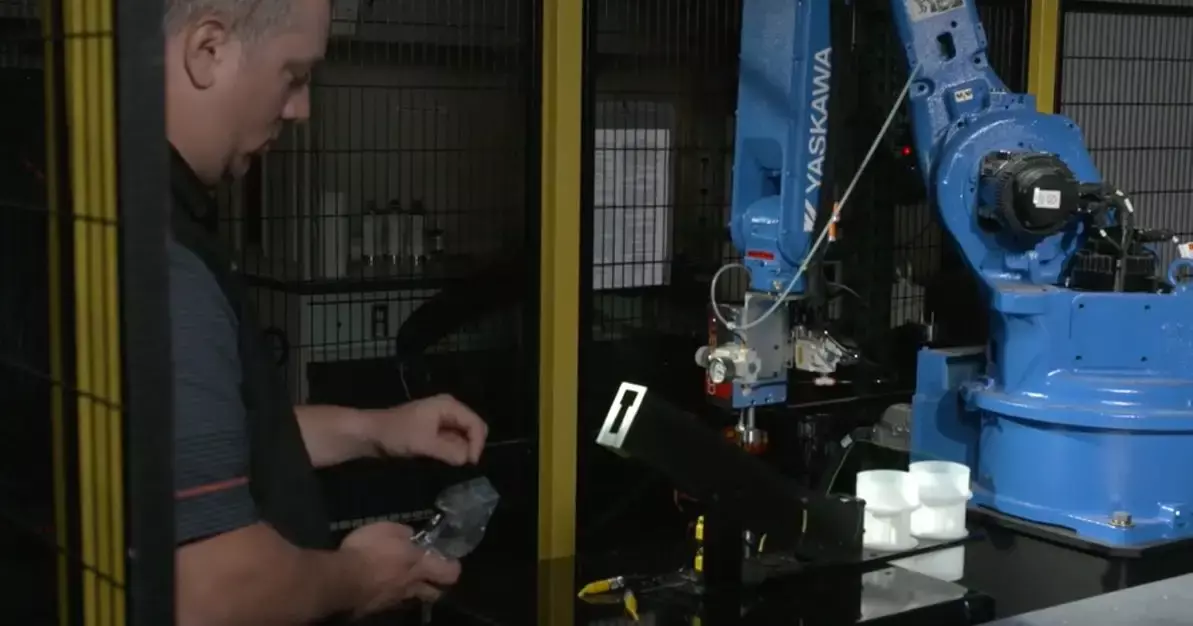
Poka Yoke Examples
Car Seat Belt Buckle
One common poka-yoke example is the seat belt buckle in cars. The buckle is designed in such a way that it can only be inserted one way, preventing users from incorrectly fastening the seatbelt. The seatbelt also includes an alarm that sounds if the buckle is not securely fastened, alerting the driver to take action.
USB Connector
Another poka-yoke example is the USB connector. USB connectors are designed with a specific shape and size that can only be inserted one way. This prevents users from trying to force the connector in the wrong way, which can damage the device or the connector itself.
Coffee Maker
A coffee maker can also be designed with poka-yoke principles in mind. For example, some coffee makers include a mechanism that prevents the user from accidentally brewing coffee without a cup in place. This helps avoid spills and reduce the risk of burns caused by hot coffee.
Poka Yoke & Fluid Applicators
The process of fluid application is a complex one, involving more than just the simple act of applying fluid to a substrate. In fact, there are multiple steps that take place both before and after the fluid is applied, each of which presents an opportunity for errors to occur. These steps can include wetting out the applicator before use, replacing the applicator after the fluid is dispensed, and ensuring the fluid is dispensed at the correct rate and in the correct amount.
Even with a fully automated application system, errors can still occur. For example, an operator might accidentally insert the wrong type of applicator, leading to improper fluid application and potentially damaging the substrate. Or the system might fail to detect when an applicator is worn out and needs to be replaced, leading to inconsistent or inaccurate fluid application.
To prevent these errors and ensure consistent, high-quality fluid application, manufacturers can implement poka-yoke principles and methods. These can include:
- Designing applicators and components with poka-yoke in mind: By designing applicators and components with unique shapes or sizes that only fit together in one way, manufacturers can reduce the likelihood of errors occurring during assembly.
- Implementing visual indicators: Color-coded components or other visual indicators can help operators identify the correct parts to use, reducing opportunities for mistakes.
- Automation: Automated systems can be used to detect and correct errors in real time. For example, sensors can be used to detect when an applicator is inserted incorrectly, triggering a warning or correction mechanism to prevent the error from causing further problems.
- Testing and inspection: Quality control measures can be put in place to ensure that applicators are dispensing the correct amount of fluid, minimizing the risk or over- or under-dispensing.
Conclusion
In today’s manufacturing environment, no process is completely error-proof. That’s why industry leaders around the world have adopted lean manufacturing and Six Sigma tools to help minimize errors and waste, and optimize productivity. At Designetics, we recognize the importance of these principles and have incorporated them into the design of our fluid applicators and automated fluid application systems.
Our focus on poka-yoke, a key principle of Lean and Six Sigma, helps to ensure that errors are prevented before they occur. This can help you to improve quality, reduce scrap and rework, and increase overall productivity. By designing our fluid applicators with unique shapes or sizes that only fit together in one way, we can reduce the likelihood of errors occurring during assembly. Additionally, we can implement visual indicators and automated systems to detect and correct errors in real-time, helping to prevent issues from snowballing into larger problems.
If you’re looking to streamline your fluid application process and minimize the risk of errors, Designetics can help. Our team of experts can work with you to develop customized solutions that meet your unique needs and requirements. Contact us today to learn more about how we can help you achieve error-free fluid application.
Ready to Error-Proof Your Fluid Application Process?
Designetics’ automated fluid application systems supply fluid to a robot’s end-of-arm tooling via an applicator track. However, this seemingly simple process presents several opportunities for error that can result in scape, rework and downtime. To ensure optimal productivity and quality, our applicator track has been designed with poka-yoke principles to keep these errors from occurring.
The applicator track features two poka-yoke design elements: a warning poka-yoke and a control poka-yoke. The warning poka-yoke uses two sensors, a “low applicator” sensor and an “in-position” sensor, to alert the robot’s controller when there is a low supply of applicators or an applicator is not in the correct position, preventing collisions and downtime.
The control poka-yoke ensures that every applicator acquired by the robot is in the correct orientation for proper fluid application. The applicator track’s design allows applicators to be loaded only in the correct orientation, preventing incorrect fluid application and the resulting rework and scrap.
By implementing these poka-yoke design features, Designetics’ applicator track helps ensure error-free fluid application, reducing waste and maximizing productivity.